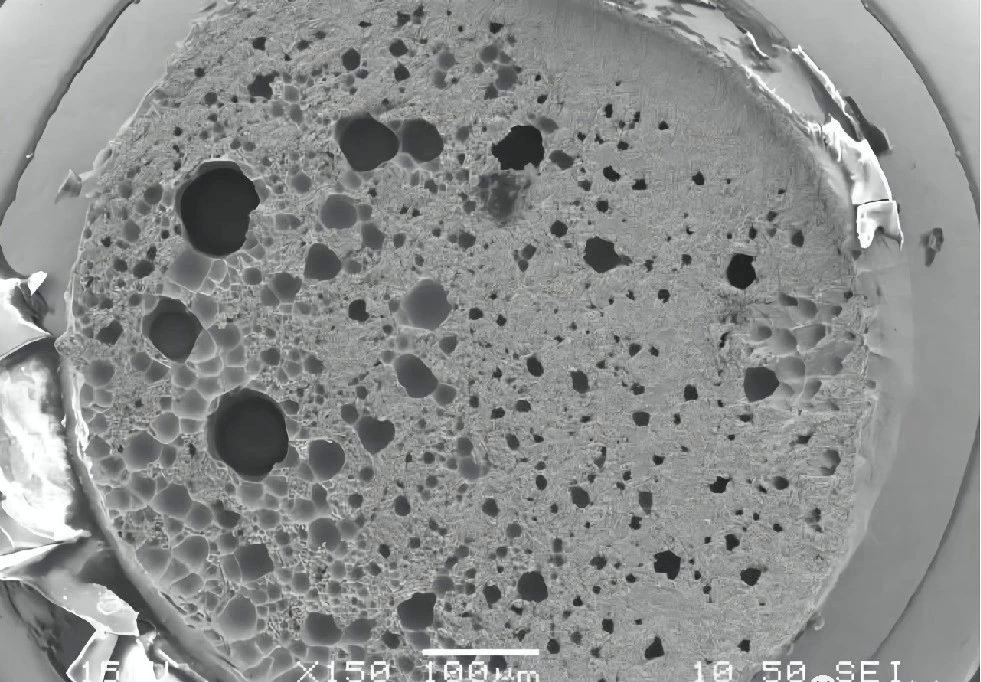
1 परिचय
सर्किट बोर्ड असेंबली में, सोल्डर पेस्ट को पहले सर्किट बोर्ड सोल्डर पैड पर मुद्रित किया जाता है, और फिर विभिन्न इलेक्ट्रॉनिक घटकों को चिपकाया जाता है। अंत में, रिफ्लो फर्नेस के बाद, सोल्डर पेस्ट में टिन मोतियों को पिघलाया जाता है और सभी प्रकार के इलेक्ट्रॉनिक घटकों और सर्किट बोर्ड के सोल्डर पैड को विद्युत सबमॉड्यूल की असेंबली का एहसास करने के लिए एक साथ वेल्ड किया जाता है। सरफेसमाउंट टेक्नोलॉजी (एसएमटी) का उपयोग उच्च-घनत्व पैकेजिंग उत्पादों में तेजी से किया जा रहा है, जैसे सिस्टम लेवल पैकेज (एसआईपी), बॉलग्रिडरे (बीजीए) डिवाइस, और पावर बेयर चिप, स्क्वायर फ्लैट पिन-कम पैकेज (क्वाड एएटीनो-लीड, जिसे क्यूएफएन कहा जाता है) ) उपकरण।
सोल्डर पेस्ट वेल्डिंग प्रक्रिया और सामग्रियों की विशेषताओं के कारण, इन बड़े सोल्डर सतह उपकरणों के रिफ्लो वेल्डिंग के बाद, सोल्डर वेल्डिंग क्षेत्र में छेद होंगे, जो उत्पाद प्रदर्शन के विद्युत गुणों, थर्मल गुणों और यांत्रिक गुणों को प्रभावित करेगा, और यहां तक कि उत्पाद की विफलता भी हो सकती है, इसलिए, सोल्डर पेस्ट रिफ्लो वेल्डिंग कैविटी को सुधारने के लिए एक प्रक्रिया और तकनीकी समस्या बन गई है जिसे हल किया जाना चाहिए, कुछ शोधकर्ताओं ने बीजीए सोल्डर बॉल वेल्डिंग कैविटी के कारणों का विश्लेषण और अध्ययन किया है, और सुधार समाधान प्रदान किए हैं, पारंपरिक सोल्डर पेस्ट रिफ्लो वेल्डिंग प्रक्रिया वेल्डिंग क्षेत्र का 10 मिमी2 से अधिक क्यूएफएन या 6 मिमी2 से अधिक वेल्डिंग क्षेत्र के नंगे चिप समाधान की कमी है।
वेल्ड छेद को बेहतर बनाने के लिए प्रीफॉर्मसोल्डर वेल्डिंग और वैक्यूम रिफ्लक्स फर्नेस वेल्डिंग का उपयोग करें। पूर्वनिर्मित सोल्डर को फ्लक्स को इंगित करने के लिए विशेष उपकरण की आवश्यकता होती है। उदाहरण के लिए, चिप को प्रीफैब्रिकेटेड सोल्डर पर सीधे रखने के बाद चिप को ऑफसेट और गंभीरता से झुकाया जाता है। यदि फ्लक्स माउंट चिप को रिफ्लो और फिर पॉइंट किया जाता है, तो प्रक्रिया दो रिफ्लो द्वारा बढ़ जाती है, और प्रीफैब्रिकेटेड सोल्डर और फ्लक्स सामग्री की लागत सोल्डर पेस्ट की तुलना में बहुत अधिक है।
वैक्यूम रिफ्लक्स उपकरण अधिक महंगे हैं, स्वतंत्र वैक्यूम चैम्बर की वैक्यूम क्षमता बहुत कम है, लागत प्रदर्शन अधिक नहीं है, और टिन छींटे की समस्या गंभीर है, जो उच्च-घनत्व और छोटे-पिच के अनुप्रयोग में एक महत्वपूर्ण कारक है उत्पाद. इस पेपर में, पारंपरिक सोल्डर पेस्ट रिफ्लो वेल्डिंग प्रक्रिया के आधार पर, वेल्डिंग कैविटी को बेहतर बनाने और वेल्डिंग कैविटी के कारण होने वाली बॉन्डिंग और प्लास्टिक सील क्रैकिंग की समस्याओं को हल करने के लिए एक नई सेकेंडरी रिफ्लो वेल्डिंग प्रक्रिया विकसित और शुरू की गई है।
2 सोल्डर पेस्ट प्रिंटिंग रिफ्लो वेल्डिंग कैविटी और उत्पादन तंत्र
2.1 वेल्डिंग कैविटी
रिफ्लो वेल्डिंग के बाद, उत्पाद का एक्स-रे के तहत परीक्षण किया गया। हल्के रंग वाले वेल्डिंग क्षेत्र में छेद वेल्डिंग परत में अपर्याप्त सोल्डर के कारण पाए गए, जैसा कि चित्र 1 में दिखाया गया है।
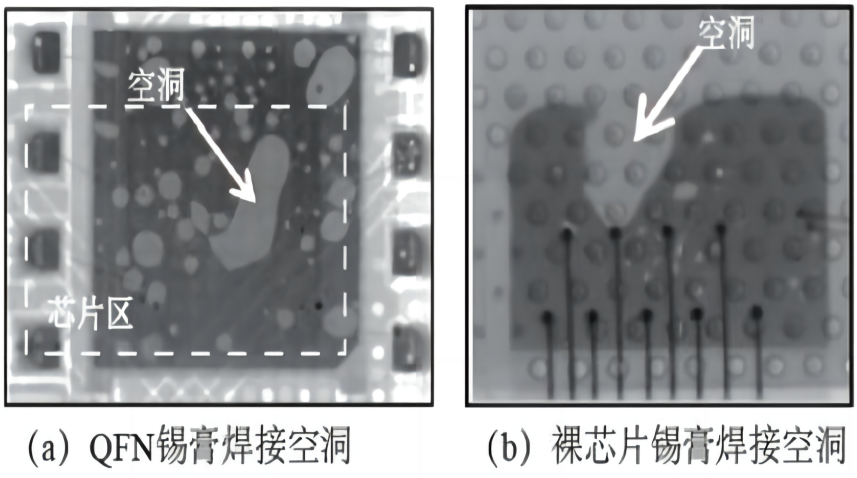
बुलबुले के छेद का एक्स-रे पता लगाना
2.2 वेल्डिंग कैविटी का गठन तंत्र
उदाहरण के तौर पर एसएसी305 सोल्डर पेस्ट को लेते हुए, मुख्य संरचना और कार्य तालिका 1 में दिखाए गए हैं। फ्लक्स और टिन मोतियों को पेस्ट के आकार में एक साथ बांधा गया है। टिन सोल्डर और फ्लक्स का वजन अनुपात लगभग 9:1 है, और आयतन अनुपात लगभग 1:1 है।
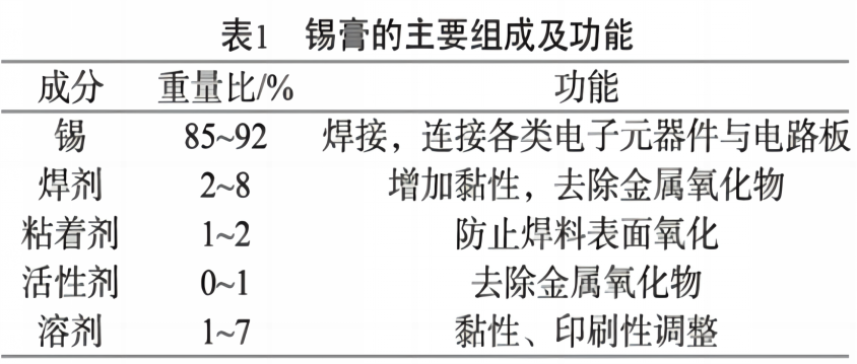
सोल्डर पेस्ट को मुद्रित करने और विभिन्न इलेक्ट्रॉनिक घटकों के साथ माउंट करने के बाद, सोल्डर पेस्ट रिफ्लक्स भट्टी से गुजरने पर प्रीहीटिंग, सक्रियण, रिफ्लक्स और कूलिंग के चार चरणों से गुजरेगा। अलग-अलग चरणों में अलग-अलग तापमान के साथ सोल्डर पेस्ट की स्थिति भी अलग-अलग होती है, जैसा चित्र 2 में दिखाया गया है।
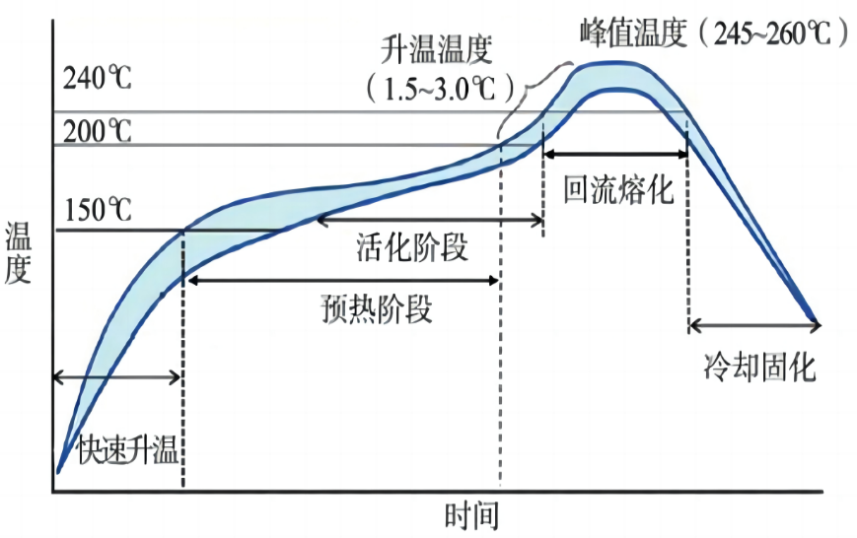
रिफ़्लो सोल्डरिंग के प्रत्येक क्षेत्र के लिए प्रोफ़ाइल संदर्भ
प्रीहीटिंग और सक्रियण चरण में, सोल्डर पेस्ट में फ्लक्स में अस्थिर घटक गर्म होने पर गैस में बदल जाएंगे। उसी समय, वेल्डिंग परत की सतह पर ऑक्साइड हटा दिए जाने पर गैसें उत्पन्न होंगी। इनमें से कुछ गैसें अस्थिर हो जाएंगी और सोल्डर पेस्ट छोड़ देंगी, और फ्लक्स के अस्थिरता के कारण सोल्डर मोती कसकर संघनित हो जाएंगे। रिफ्लक्स चरण में, सोल्डर पेस्ट में शेष फ्लक्स जल्दी से वाष्पित हो जाएगा, टिन के मोती पिघल जाएंगे, थोड़ी मात्रा में फ्लक्स वाष्पशील गैस और टिन मोतियों के बीच की अधिकांश हवा समय पर नहीं बिखरेगी, और अवशेष में पिघला हुआ टिन और पिघले हुए टिन के तनाव के तहत हैमबर्गर सैंडविच संरचना होती है और सर्किट बोर्ड सोल्डर पैड और इलेक्ट्रॉनिक घटकों द्वारा पकड़ी जाती है, और तरल टिन में लिपटी गैस से बचना मुश्किल होता है केवल ऊपर की ओर उछाल के कारण ऊपरी पिघलने का समय बहुत कम होता है। जब पिघला हुआ टिन ठंडा हो जाता है और ठोस टिन बन जाता है, तो वेल्डिंग परत में छिद्र दिखाई देते हैं और सोल्डर छेद बनते हैं, जैसा कि चित्र 3 में दिखाया गया है।
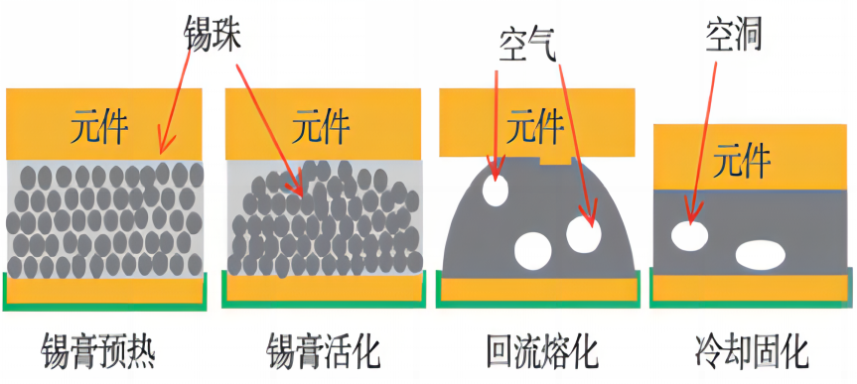
सोल्डर पेस्ट रिफ्लो वेल्डिंग द्वारा उत्पन्न शून्य का योजनाबद्ध आरेख
वेल्डिंग कैविटी का मूल कारण यह है कि सोल्डर पेस्ट में लिपटी हवा या वाष्पशील गैस पिघलने के बाद पूरी तरह से डिस्चार्ज नहीं होती है। प्रभावित करने वाले कारकों में सोल्डर पेस्ट सामग्री, सोल्डर पेस्ट प्रिंटिंग आकार, सोल्डर पेस्ट प्रिंटिंग मात्रा, रिफ्लक्स तापमान, रिफ्लक्स समय, वेल्डिंग आकार, संरचना इत्यादि शामिल हैं।
3. सोल्डर पेस्ट प्रिंटिंग रिफ्लो वेल्डिंग होल के प्रभावित करने वाले कारकों का सत्यापन
क्यूएफएन और बेयर चिप परीक्षणों का उपयोग रिफ्लो वेल्डिंग रिक्तियों के मुख्य कारणों की पुष्टि करने और सोल्डर पेस्ट द्वारा मुद्रित रिफ्लो वेल्डिंग रिक्तियों को सुधारने के तरीके खोजने के लिए किया गया था। क्यूएफएन और बेअर चिप सोल्डर पेस्ट रीफ्लो वेल्डिंग उत्पाद प्रोफ़ाइल चित्र 4 में दिखाई गई है, क्यूएफएन वेल्डिंग सतह का आकार 4.4 मिमीx4.1 मिमी है, वेल्डिंग सतह टिनड परत (100% शुद्ध टिन) है; नंगे चिप का वेल्डिंग आकार 3.0 मिमीx2.3 मिमी है, वेल्डिंग परत स्पटर निकल-वैनेडियम बाईमेटेलिक परत है, और सतह परत वैनेडियम है। सब्सट्रेट का वेल्डिंग पैड इलेक्ट्रोलेस निकल-पैलेडियम गोल्ड-डिपिंग था, और मोटाई 0.4μm/0.06μm/0.04μm थी। SAC305 सोल्डर पेस्ट का उपयोग किया जाता है, सोल्डर पेस्ट प्रिंटिंग उपकरण DEK होराइजन APIx है, रिफ्लक्स फर्नेस उपकरण BTUPyramax150N है, और एक्स-रे उपकरण DAGExD7500VR है।
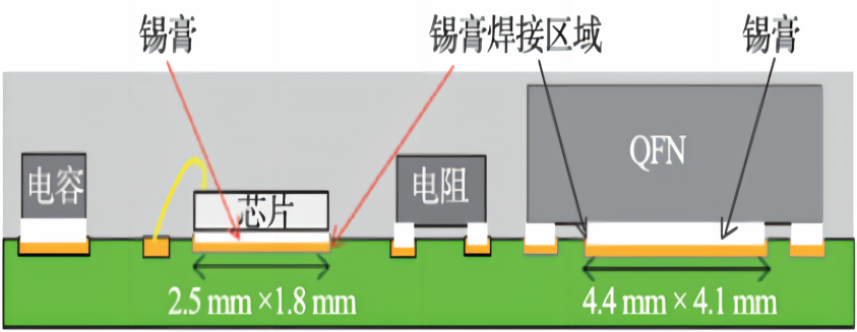
क्यूएफएन और नंगे चिप वेल्डिंग चित्र
परीक्षण परिणामों की तुलना की सुविधा के लिए, तालिका 2 में दी गई शर्तों के तहत रिफ्लो वेल्डिंग का प्रदर्शन किया गया।
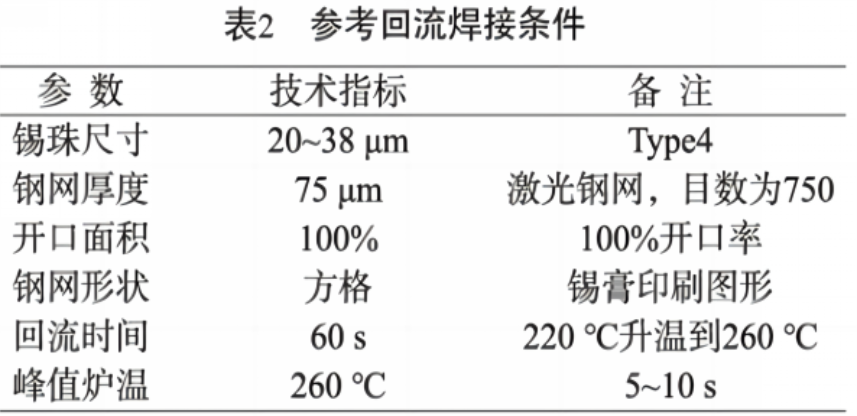
रीफ़्लो वेल्डिंग स्थिति तालिका
सतह पर माउंटिंग और रिफ्लो वेल्डिंग पूरी होने के बाद, एक्स-रे द्वारा वेल्डिंग परत का पता लगाया गया, और यह पाया गया कि क्यूएफएन और नंगे चिप के नीचे वेल्डिंग परत में बड़े छेद थे, जैसा कि चित्र 5 में दिखाया गया है।
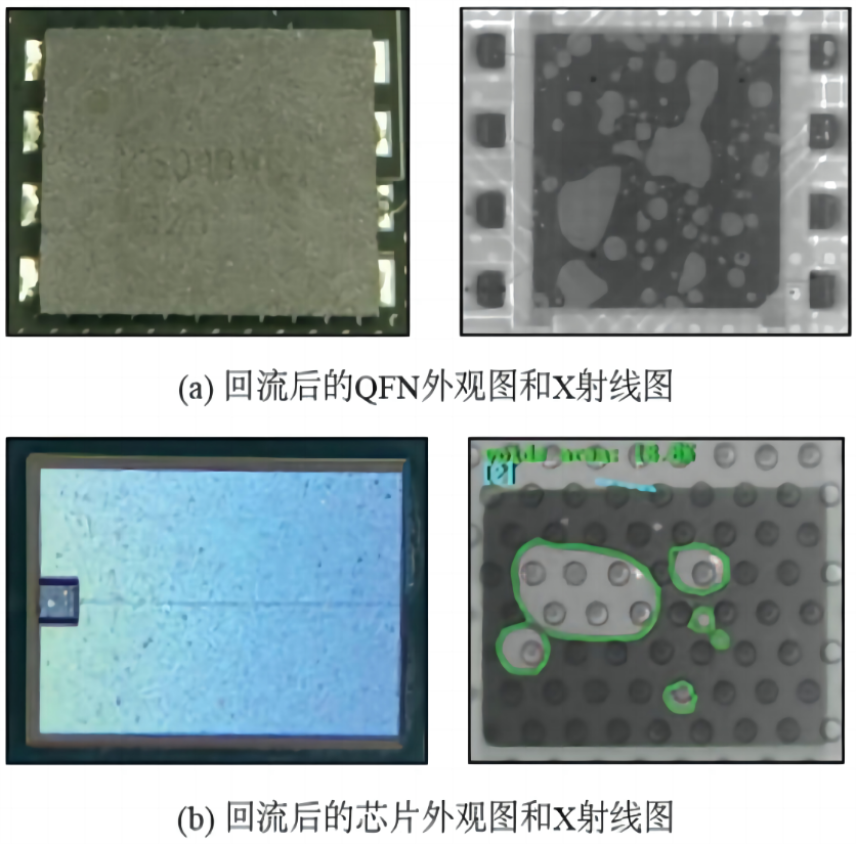
क्यूएफएन और चिप होलोग्राम (एक्स-रे)
चूंकि टिन मनका आकार, स्टील जाल मोटाई, उद्घाटन क्षेत्र दर, स्टील जाल आकार, रिफ्लक्स समय और पीक फर्नेस तापमान सभी रिफ्लो वेल्डिंग रिक्तियों को प्रभावित करेंगे, ऐसे कई प्रभावशाली कारक हैं, जिन्हें सीधे डीओई परीक्षण द्वारा सत्यापित किया जाएगा, और प्रयोगात्मक की संख्या समूह बहुत बड़े होंगे. सहसंबंध तुलना परीक्षण के माध्यम से मुख्य प्रभावशाली कारकों को जल्दी से स्क्रीन करना और निर्धारित करना आवश्यक है, और फिर डीओई के माध्यम से मुख्य प्रभावशाली कारकों को और अनुकूलित करना आवश्यक है।
3.1 सोल्डर छेद और सोल्डर पेस्ट टिन मोतियों के आयाम
टाइप3 (बीड आकार 25-45 माइक्रोमीटर) एसएसी305 सोल्डर पेस्ट परीक्षण के साथ, अन्य स्थितियां अपरिवर्तित रहती हैं। रिफ्लो के बाद, सोल्डर परत में छेदों को मापा जाता है और टाइप4 सोल्डर पेस्ट के साथ तुलना की जाती है। यह पाया गया है कि सोल्डर परत में छेद दो प्रकार के सोल्डर पेस्ट के बीच महत्वपूर्ण रूप से भिन्न नहीं होते हैं, यह दर्शाता है कि अलग-अलग मनका आकार वाले सोल्डर पेस्ट का सोल्डर परत में छेद पर कोई स्पष्ट प्रभाव नहीं पड़ता है, जो एक प्रभावशाली कारक नहीं है। जैसा कि चित्र में दिखाया गया है। 6 जैसा दिखाया गया है.
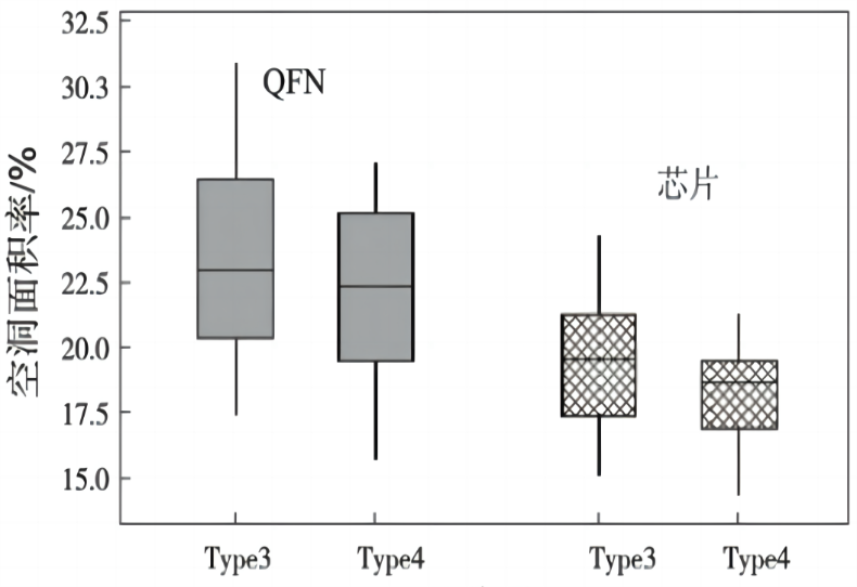
विभिन्न कण आकारों के साथ धातु टिन पाउडर छेद की तुलना
3.2 वेल्डिंग कैविटी और मुद्रित स्टील जाल की मोटाई
रिफ्लो के बाद, वेल्डेड परत के गुहा क्षेत्र को 50 माइक्रोन, 100 माइक्रोन और 125 माइक्रोन की मोटाई के साथ मुद्रित स्टील जाल से मापा गया, और अन्य स्थितियां अपरिवर्तित रहीं। यह पाया गया कि क्यूएफएन पर स्टील जाल (सोल्डर पेस्ट) की विभिन्न मोटाई के प्रभाव की तुलना 75 माइक्रोन की मोटाई के साथ मुद्रित स्टील जाल से की गई थी। जैसे-जैसे स्टील जाल की मोटाई बढ़ती है, गुहा क्षेत्र धीरे-धीरे कम होता जाता है। एक निश्चित मोटाई (100μm) तक पहुंचने के बाद, गुहा क्षेत्र उल्टा हो जाएगा और स्टील जाल की मोटाई बढ़ने के साथ बढ़ना शुरू हो जाएगा, जैसा कि चित्र 7 में दिखाया गया है।
इससे पता चलता है कि जब सोल्डर पेस्ट की मात्रा बढ़ जाती है, तो रिफ्लक्स वाला तरल टिन चिप से ढक जाता है, और अवशिष्ट वायु निकास का आउटलेट केवल चार तरफ संकीर्ण होता है। जब सोल्डर पेस्ट की मात्रा बदल जाती है, तो अवशिष्ट वायु निकास का आउटलेट भी बढ़ जाता है, और तरल टिन में लिपटी हवा के तत्काल फटने या तरल टिन से निकलने वाली वाष्पशील गैस के कारण तरल टिन क्यूएफएन और चिप के चारों ओर फैल जाएगा।
परीक्षण में पाया गया कि स्टील की जाली की मोटाई बढ़ने के साथ, हवा या वाष्पशील गैस के निकलने के कारण बुलबुला फटने की संभावना भी बढ़ जाएगी, और क्यूएफएन और चिप के आसपास टिन के छींटे पड़ने की संभावना भी तदनुसार बढ़ जाएगी।
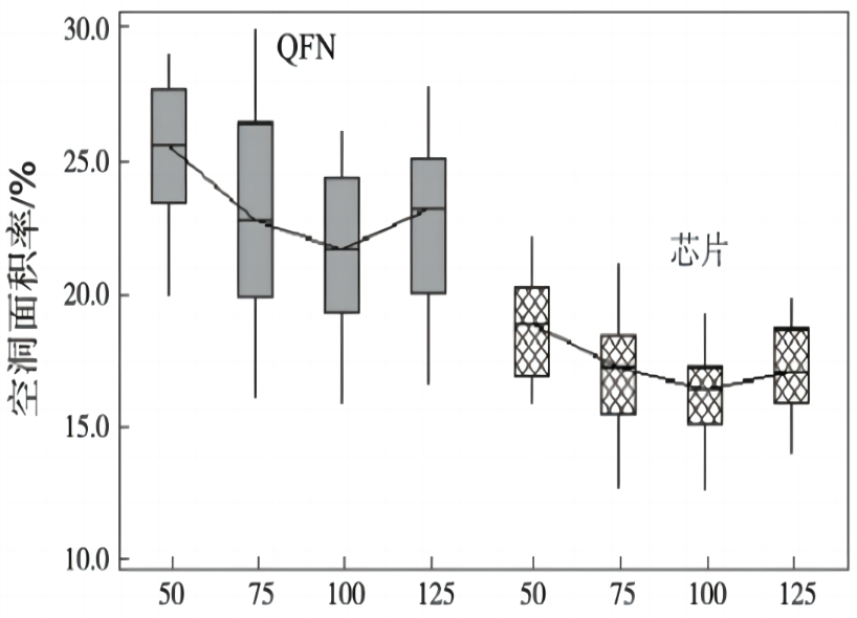
विभिन्न मोटाई के स्टील जाल में छेद की तुलना
3.3 वेल्डिंग कैविटी और स्टील मेश ओपनिंग का क्षेत्र अनुपात
100%, 90% और 80% की शुरुआती दर के साथ मुद्रित स्टील जाल का परीक्षण किया गया, और अन्य स्थितियां अपरिवर्तित रहीं। रिफ्लो के बाद, वेल्डेड परत के गुहा क्षेत्र को मापा गया और 100% उद्घाटन दर के साथ मुद्रित स्टील जाल के साथ तुलना की गई। यह पाया गया कि 100% और 90% 80% की शुरुआती दर की शर्तों के तहत वेल्डेड परत की गुहा में कोई महत्वपूर्ण अंतर नहीं था, जैसा कि चित्र 8 में दिखाया गया है।
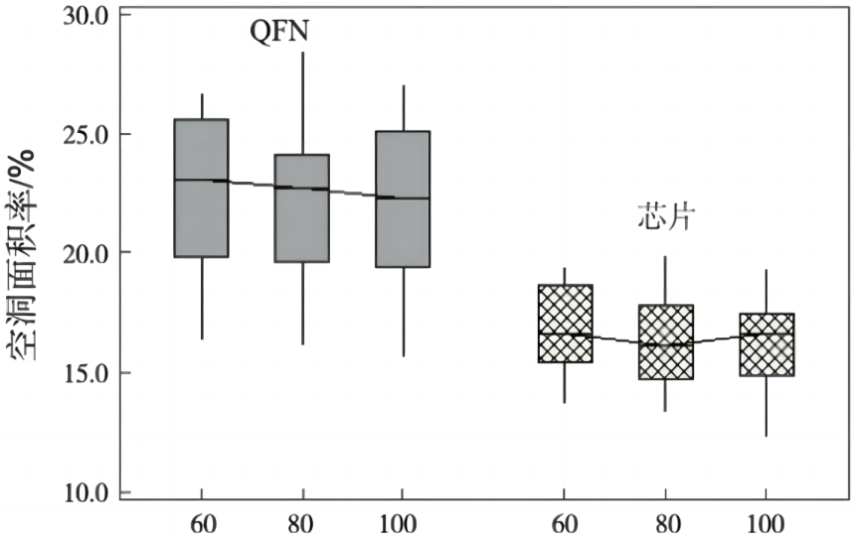
विभिन्न स्टील जाल के विभिन्न उद्घाटन क्षेत्र की गुहा तुलना
3.4 वेल्डेड कैविटी और मुद्रित स्टील जाल आकार
स्ट्रिप बी और झुके हुए ग्रिड सी के सोल्डर पेस्ट के मुद्रण आकार परीक्षण के साथ, अन्य स्थितियाँ अपरिवर्तित रहती हैं। रिफ्लो के बाद, वेल्डिंग परत के गुहा क्षेत्र को मापा जाता है और ग्रिड ए के मुद्रण आकार के साथ तुलना की जाती है। यह पाया गया है कि ग्रिड, स्ट्रिप और इच्छुक ग्रिड की स्थितियों के तहत वेल्डिंग परत की गुहा में कोई महत्वपूर्ण अंतर नहीं है, जैसा कि चित्र 9 में दिखाया गया है।
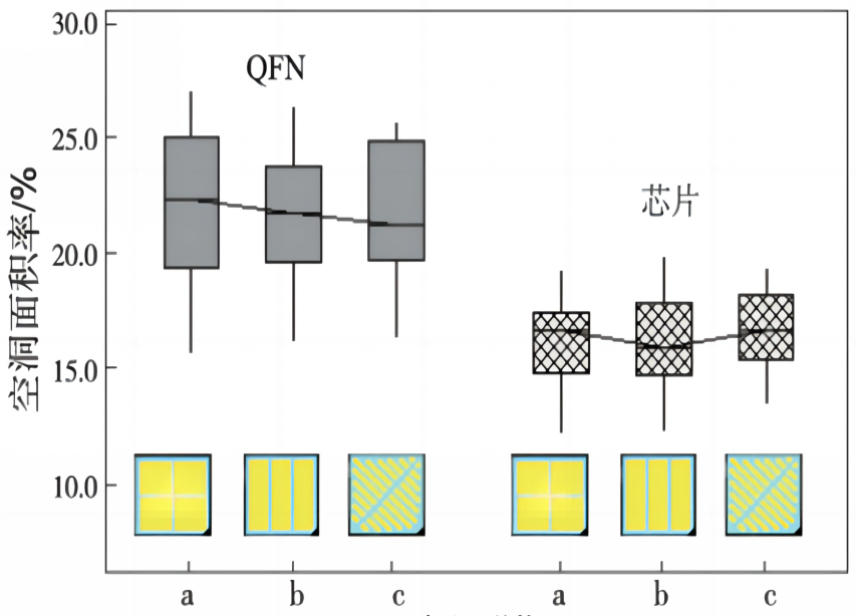
स्टील जाल के विभिन्न उद्घाटन मोड में छेद की तुलना
3.5 वेल्डिंग कैविटी और रिफ्लक्स समय
लंबे समय तक रिफ्लक्स समय (70 एस, 80 एस, 90 एस) परीक्षण के बाद, अन्य स्थितियां अपरिवर्तित रहती हैं, वेल्डिंग परत में छेद को रिफ्लक्स के बाद मापा गया था, और 60 एस के रिफ्लक्स समय के साथ तुलना की गई, यह पाया गया कि वृद्धि के साथ भाटा समय, वेल्डिंग छेद क्षेत्र में कमी आई, लेकिन समय की वृद्धि के साथ कमी का आयाम धीरे-धीरे कम हो गया, जैसा कि चित्र 10 में दिखाया गया है। इससे पता चलता है कि अपर्याप्त भाटा समय के मामले में, बढ़ रहा है भाटा समय पिघले हुए तरल टिन में लिपटी हवा के पूर्ण अतिप्रवाह के लिए अनुकूल है, लेकिन भाटा समय एक निश्चित समय तक बढ़ने के बाद, तरल टिन में लिपटी हवा का फिर से अतिप्रवाह करना मुश्किल होता है। रिफ्लक्स समय वेल्डिंग कैविटी को प्रभावित करने वाले कारकों में से एक है।
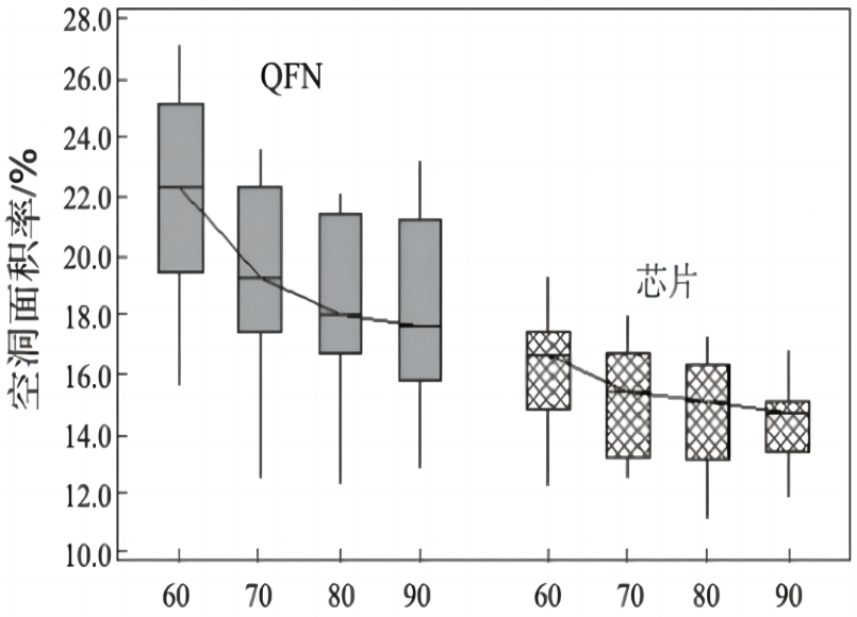
विभिन्न भाटा समय लंबाई की शून्य तुलना
3.6 वेल्डिंग कैविटी और चरम भट्ठी का तापमान
240 ℃ और 250 ℃ शिखर भट्टी तापमान परीक्षण और अन्य अपरिवर्तित स्थितियों के साथ, वेल्डेड परत के गुहा क्षेत्र को रिफ्लो के बाद मापा गया था, और 260 ℃ शिखर भट्टी तापमान के साथ तुलना की गई, यह पाया गया कि विभिन्न शिखर भट्टी तापमान स्थितियों के तहत, की गुहा क्यूएफएन और चिप की वेल्डेड परत में महत्वपूर्ण बदलाव नहीं हुआ, जैसा कि चित्र 11 में दिखाया गया है। यह दर्शाता है कि अलग-अलग शिखर भट्ठी के तापमान का क्यूएफएन और वेल्डिंग परत में छेद पर कोई स्पष्ट प्रभाव नहीं पड़ता है चिप का, जो कोई प्रभावशाली कारक नहीं है।
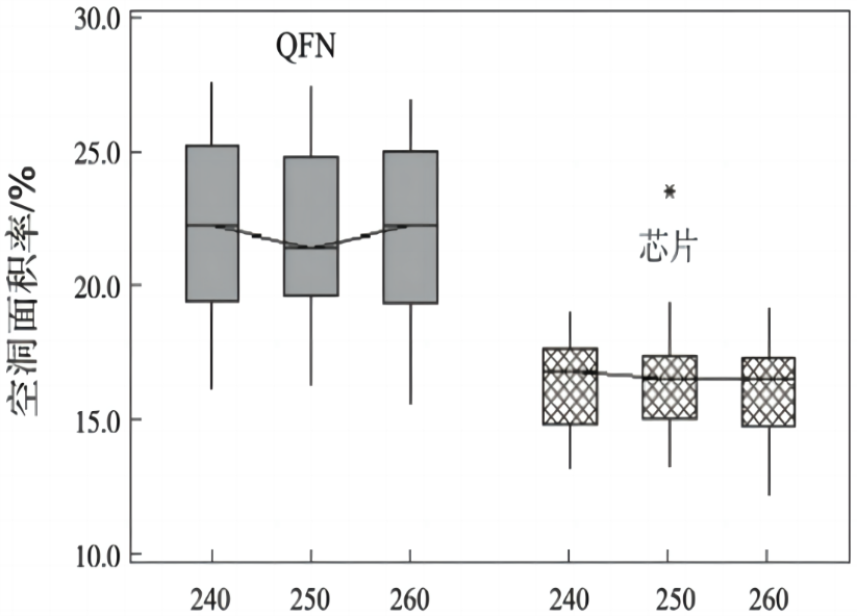
विभिन्न चरम तापमानों की शून्य तुलना
उपरोक्त परीक्षणों से संकेत मिलता है कि क्यूएफएन और चिप की वेल्ड परत गुहा को प्रभावित करने वाले महत्वपूर्ण कारक रिफ्लक्स समय और स्टील जाल की मोटाई हैं।
4 सोल्डर पेस्ट प्रिंटिंग रिफ्लो वेल्डिंग कैविटी में सुधार
वेल्डिंग कैविटी में सुधार के लिए 4.1DOE परीक्षण
मुख्य प्रभावित करने वाले कारकों (रिफ्लक्स समय और स्टील जाल मोटाई) का इष्टतम मूल्य ढूंढकर क्यूएफएन और चिप की वेल्डिंग परत में छेद में सुधार किया गया था। सोल्डर पेस्ट SAC305 प्रकार 4 था, स्टील जाल का आकार ग्रिड प्रकार (100% उद्घाटन डिग्री) था, शिखर भट्ठी का तापमान 260 ℃ था, और अन्य परीक्षण स्थितियां परीक्षण उपकरण के समान थीं। डीओई परीक्षण और परिणाम तालिका 3 में दिखाए गए थे। क्यूएफएन और चिप वेल्डिंग छेद पर स्टील जाल मोटाई और रिफ्लक्स समय के प्रभाव चित्र 12 में दिखाए गए हैं। मुख्य प्रभावशाली कारकों के इंटरैक्शन विश्लेषण के माध्यम से, यह पाया गया है कि 100 माइक्रोन स्टील जाल मोटाई का उपयोग करना और 80 एस रिफ्लक्स समय क्यूएफएन और चिप की वेल्डिंग कैविटी को काफी कम कर सकता है। क्यूएफएन की वेल्डिंग कैविटी दर अधिकतम 27.8% से घटाकर 16.1% कर दी गई है, और चिप की वेल्डिंग कैविटी दर अधिकतम 20.5% से घटाकर 14.5% कर दी गई है।
परीक्षण में, 1000 उत्पाद इष्टतम परिस्थितियों (100 माइक्रोन स्टील जाल मोटाई, 80 एस रिफ्लक्स समय) के तहत उत्पादित किए गए थे, और 100 क्यूएफएन और चिप की वेल्डिंग कैविटी दर को यादृच्छिक रूप से मापा गया था। क्यूएफएन की औसत वेल्डिंग कैविटी दर 16.4% थी, और चिप की औसत वेल्डिंग कैविटी दर 14.7% थी। चिप और चिप की वेल्ड कैविटी दर स्पष्ट रूप से कम हो गई है।
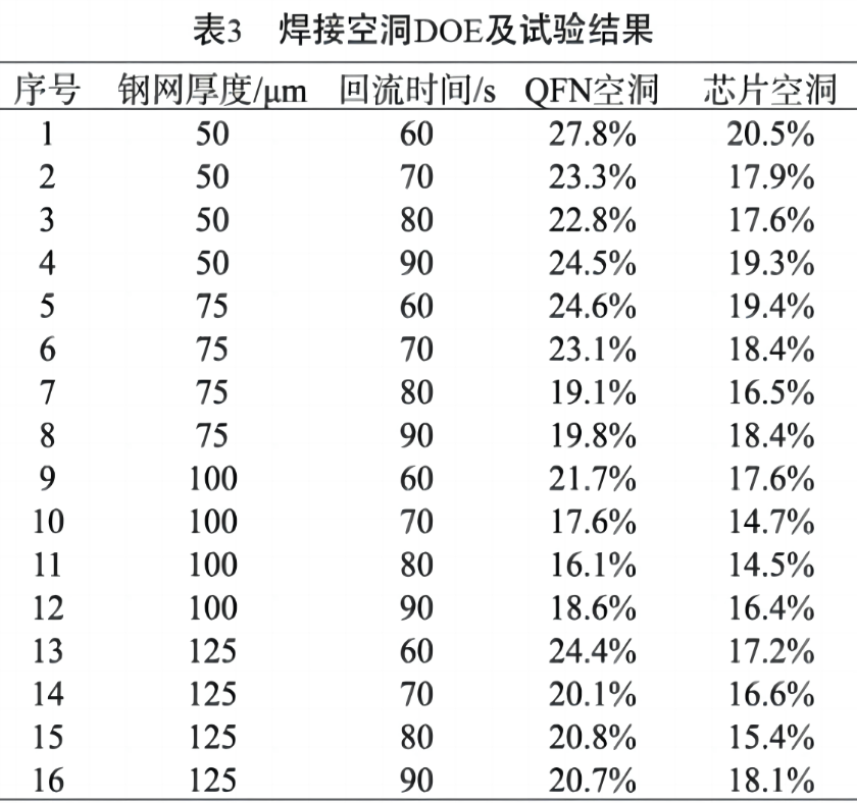
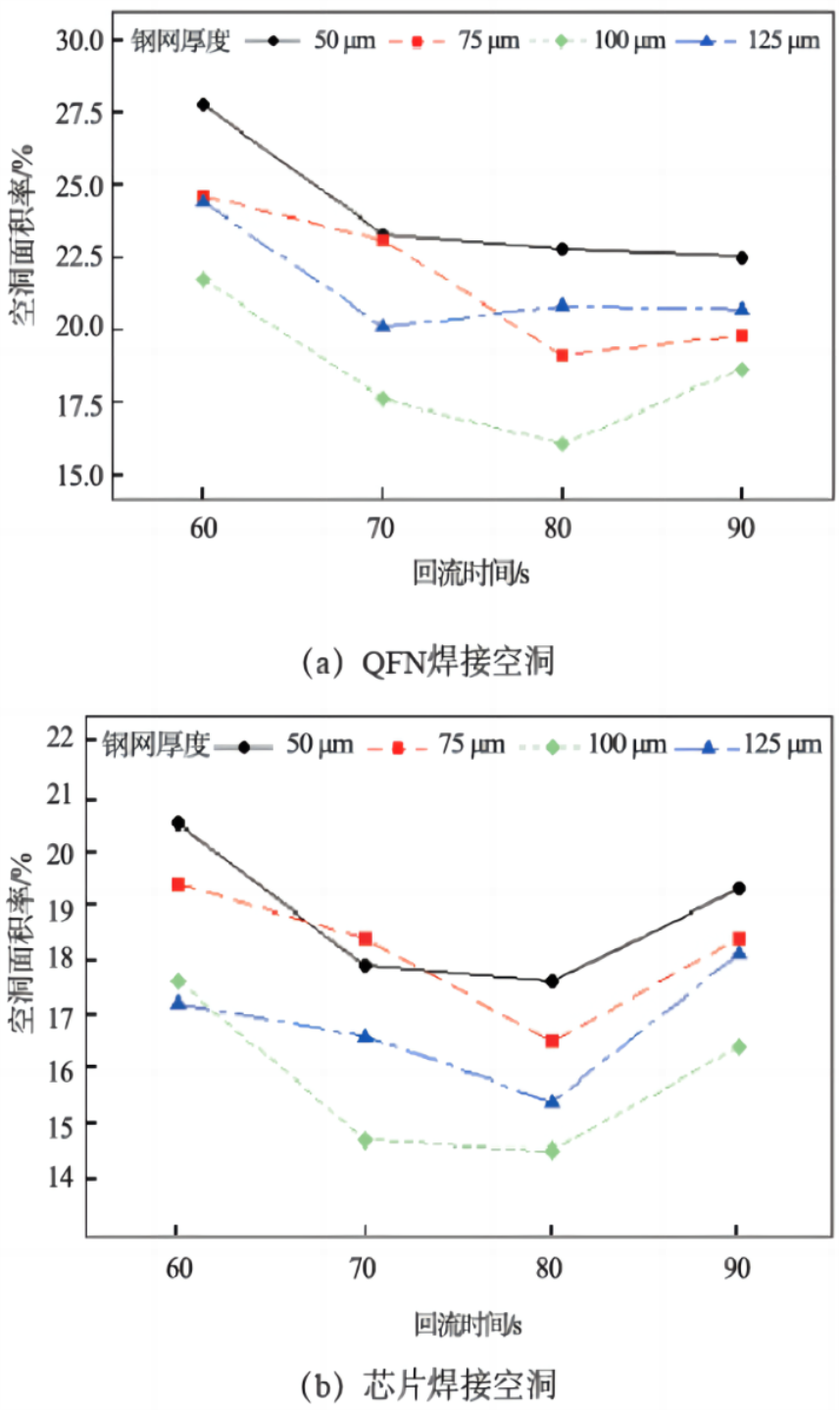
4.2 नई प्रक्रिया वेल्डिंग कैविटी में सुधार करती है
वास्तविक उत्पादन स्थिति और परीक्षण से पता चलता है कि जब चिप के नीचे वेल्डिंग कैविटी क्षेत्र 10% से कम होता है, तो लीड बॉन्डिंग और मोल्डिंग के दौरान चिप कैविटी स्थिति क्रैकिंग की समस्या नहीं होगी। डीओई द्वारा अनुकूलित प्रक्रिया पैरामीटर पारंपरिक सोल्डर पेस्ट रिफ्लो वेल्डिंग में छेदों के विश्लेषण और समाधान की आवश्यकताओं को पूरा नहीं कर सकते हैं, और चिप की वेल्डिंग कैविटी क्षेत्र दर को और कम करने की आवश्यकता है।
चूंकि सोल्डर पर लगी चिप सोल्डर में मौजूद गैस को बाहर निकलने से रोकती है, सोल्डर लेपित गैस को हटाकर या कम करके चिप के नीचे छेद की दर को और कम कर दिया जाता है। दो सोल्डर पेस्ट प्रिंटिंग के साथ रिफ्लो वेल्डिंग की एक नई प्रक्रिया अपनाई गई है: एक सोल्डर पेस्ट प्रिंटिंग, एक रिफ्लो जो क्यूएफएन को कवर नहीं करता है और सोल्डर में गैस का निर्वहन करने वाली नंगी चिप; सेकेंडरी सोल्डर पेस्ट प्रिंटिंग, पैच और सेकेंडरी रिफ्लक्स की विशिष्ट प्रक्रिया चित्र 13 में दिखाई गई है।
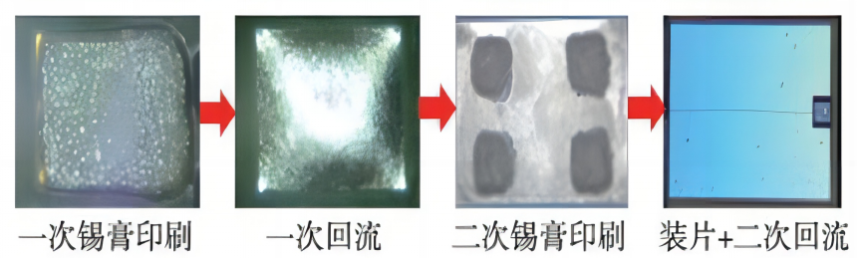
जब 75μm मोटा सोल्डर पेस्ट पहली बार मुद्रित किया जाता है, तो चिप कवर के बिना सोल्डर में अधिकांश गैस सतह से निकल जाती है, और रिफ्लक्स के बाद की मोटाई लगभग 50μm होती है। प्राथमिक रिफ्लक्स के पूरा होने के बाद, ठंडे ठोस सोल्डर की सतह पर छोटे वर्ग मुद्रित किए जाते हैं (सोल्डर पेस्ट की मात्रा को कम करने, गैस स्पिलओवर की मात्रा को कम करने, सोल्डर स्पैटर को कम करने या खत्म करने के लिए), और सोल्डर पेस्ट के साथ 50 μm की मोटाई (उपरोक्त परीक्षण परिणाम बताते हैं कि 100 μm सबसे अच्छा है, इसलिए द्वितीयक मुद्रण की मोटाई 100 μm है। 50 μm=50 μm), फिर चिप स्थापित करें, और फिर 80 सेकंड के बाद वापस लौटें। पहली प्रिंटिंग और रिफ्लो के बाद सोल्डर में लगभग कोई छेद नहीं होता है, और दूसरी प्रिंटिंग में सोल्डर पेस्ट छोटा होता है, और वेल्डिंग छेद छोटा होता है, जैसा चित्र 14 में दिखाया गया है।
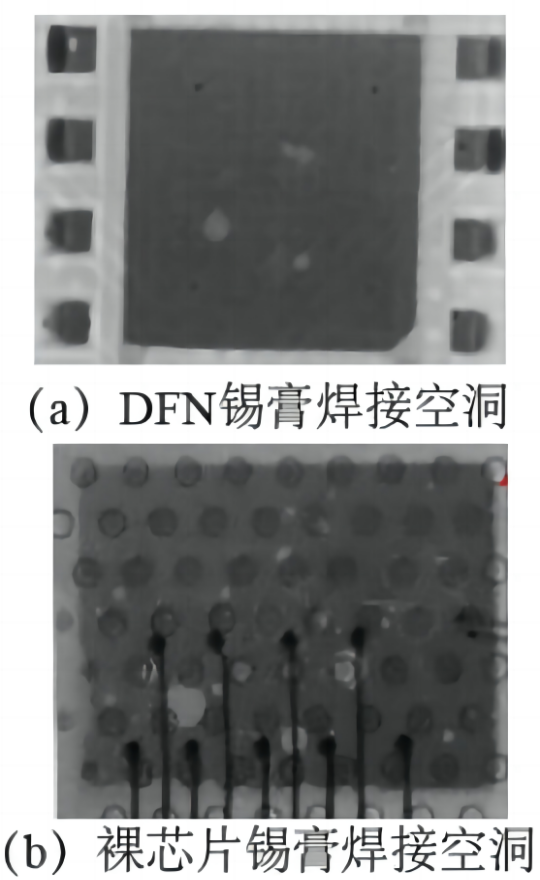
सोल्डर पेस्ट की दो छपाई के बाद, खोखली ड्राइंग
4.3 वेल्डिंग कैविटी प्रभाव का सत्यापन
2000 उत्पादों का उत्पादन (पहले प्रिंटिंग स्टील जाल की मोटाई 75 माइक्रोन है, दूसरे प्रिंटिंग स्टील जाल की मोटाई 50 माइक्रोन है), अन्य स्थितियां अपरिवर्तित हैं, 500 क्यूएफएन और चिप वेल्डिंग गुहा दर का यादृच्छिक माप, नई प्रक्रिया में पाया गया पहले रिफ्लक्स के बाद कोई कैविटी नहीं, दूसरे रिफ्लक्स QFN के बाद अधिकतम वेल्डिंग कैविटी दर 4.8% है, और चिप की अधिकतम वेल्डिंग कैविटी दर 4.1% है। मूल सिंगल-पेस्ट प्रिंटिंग वेल्डिंग प्रक्रिया और डीओई अनुकूलित प्रक्रिया की तुलना में, वेल्डिंग कैविटी काफी कम हो गई है, जैसा कि चित्र 15 में दिखाया गया है। सभी उत्पादों के कार्यात्मक परीक्षणों के बाद कोई चिप दरार नहीं पाई गई।
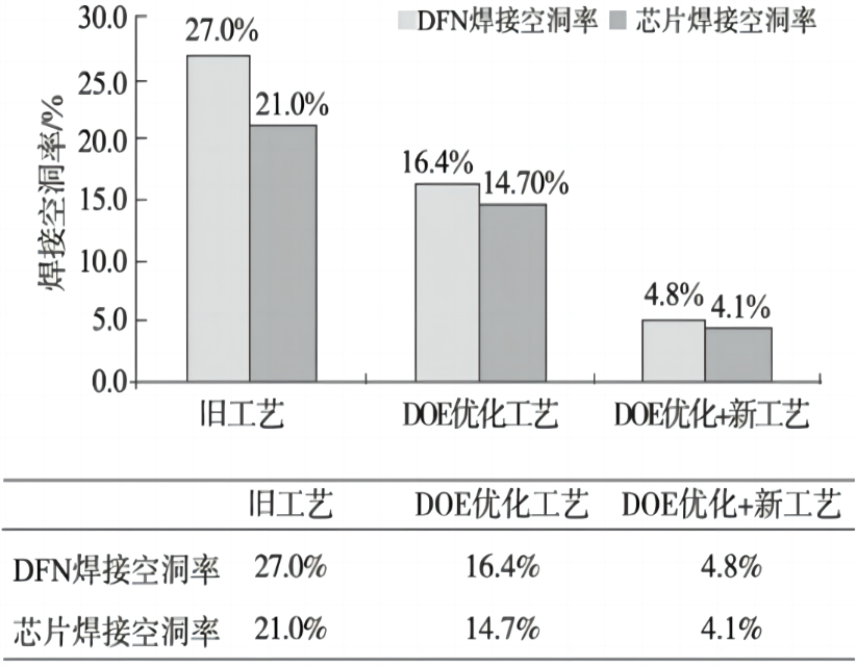
5 सारांश
सोल्डर पेस्ट प्रिंटिंग मात्रा और रिफ्लक्स समय का अनुकूलन वेल्डिंग कैविटी क्षेत्र को कम कर सकता है, लेकिन वेल्डिंग कैविटी दर अभी भी बड़ी है। दो सोल्डर पेस्ट प्रिंटिंग रिफ्लो वेल्डिंग तकनीकों का उपयोग प्रभावी ढंग से और वेल्डिंग कैविटी दर को अधिकतम कर सकता है। बड़े पैमाने पर उत्पादन में क्यूएफएन सर्किट बेयर चिप का वेल्डिंग क्षेत्र क्रमशः 4.4 मिमी x4.1 मिमी और 3.0 मिमी x2.3 मिमी हो सकता है। रिफ्लो वेल्डिंग की कैविटी दर 5% से नीचे नियंत्रित होती है, जो रिफ्लो वेल्डिंग की गुणवत्ता और विश्वसनीयता में सुधार करती है। इस पेपर में शोध बड़े क्षेत्र की वेल्डिंग सतह की वेल्डिंग कैविटी समस्या में सुधार के लिए एक महत्वपूर्ण संदर्भ प्रदान करता है।
पोस्ट करने का समय: जुलाई-05-2023